El siguiente post será para mi una bitácora personal en la que trataré de documentar mi experiencia como parte de la iniciativa de Ventiladores por Panamá. Esta iniciativa nace como un esfuerzo para brindar una respuesta a la crisis sanitaria causada por la pandemia de COVID-19 en Panamá, a través de la creación de un prototipo funcional de un ventilador mecánico de emergencia que pueda ser utilizado en un hipotético escenario en el que se agote la disponibilidad de ventiladores para atender pacientes con dificultades respiratorias provocadas por el coronavirus.
En este post trataré de recoger mis experiencia en este proyecto. Aquí publicaré imágenes del proceso de fabricación del prototipo en el que tuve la oportunidad de trabajar junto a otros miembros del equipo al que llamamos Flujo Contínuo UTP-100P. Aunque no compartiré códigos de programación ni archivos de diseño en 3D, espero publicar fotos y videos de algunos procedimientos por los que tuvimos que pasar, junto con algunas anotaciones y reflexiones personales.
Debo decir que mi participación en este proyecto se dio a través de mi vinculación con la Universidad Tecnológica de Panamá (UTP), institución en la que trabajo actualmente como docente e investigador. Fue solamente gracias a los equipos y las instalaciones disponibles en el Laboratorio de Prototipado de la Facultad de Ingeniería Eléctrica de la UTP que este proyecto pudo llevarse a cabo.
Dentro de esta iniciativa formé parte de un grupo de trabajo que incluyó a otros profesionales que hicieron aportes muy valiosos a este proyecto. De igual forma, la iniciativa Ventiladores por Panamá contó con el apoyo de profesionales de la UTP, INDICASAT, SENACYT, universidades públicas y privadas en Panamá, empresas del sector privado, profesionales médicos y veterinarios, entre muchos otros. Se trata de una iniciativa conjunta, multidisciplinaria, con aportes de diferentes sectores de la sociedad y de una gran cantidad de profesionales que donaron su tiempo y su trabao para que esto fuese posible.
Con este documento espero contar mi historia, es decir, la experiencia vista desde mi punto de vista. Estaré compartiendo información del desarrollo técnico, que fue la parte en la que se me dio la oportunidad de aportar al proyecto. Con esto quiero dejar claro que en este post no se documentará el trabajo realizado en la iniciativa de Ventiladores por Panamá, pues se dieron aporte de tantas personas, de tantos profesionales y de tantas entidades que me es imposible documentar el proyecto y hacerle justicia al aporte de todos y cada uno de los participantes de la iniciativa.
En este post trataré de documentar mi parte del trabajo. Este blog, Panama Hitek, es, hasta cierto punto, mi repositorio personal de proyectos de electrónica y programación. Como ya dije, en esta ocasión no compartiré códigos ni archivos de diseño, sino que publicaré una bitácora descriptiva del proyecto en el que participé, el cual espero que sea de ayuda para otras personas o equipos de trabajo que persigan objetivos similares a los que nos propusimos con este proyecto.
A título personal, esta será mi bitácora personal sobre el proyecto más importante en el que he tenido la oportunidad de trabajar a nivel profesional.
La situación del coronavirus en Panamá
El primer caso de la pandemia de coronavirus de 2020 en Panamá se dio el día 8 de marzo, una mujer panameña, de 40 años, quien ingreso al país en un vuelo procedente de Barajas, España.
La primera muerte fue confirmada el 10 de marzo; el paciente fallecido era el director de una escuela secundaria de Ciudad de Panamá.
El 25 de marzo se estableció una cuarentena, la cual incluyó el cierre de las oficinas públicas y privadas y la limitación de movilidad de personas por sexo y por número de cédula. Desde aquel día quedamos limitados a un periodo de dos horas los jueves y los martes, en mi caso que soy hombre. Mi hora de salida era de 5:30 PM a 7:30 PM, pues mi cédula termina en 6.
Los ciudadanos con cédula terminada en 6 teníamos como hora de salida las 6:00 PM a 7:00 PM, con la posibilidad de hacerlo 30 minutos antes de la hora hasta 30 minutos después de la hora. Esto me causó ciertas complicaciones, pues los supermercados cerraban a las 7:00 PM, razón por la cual contaba con un tiempo limitado para hacer compras. Los fines de semana no se podía salir, así que en un principio solamente tenía posibilidad de ir al supermercado 2 veces a la semana.
Antecedentes de la iniciativa de Ventiladores por Panamá
En los primeros días desde que inició la pandemia en Panamá, la Secretaría Nacional de Ciencia, Tecnología e Innovación (SENACYT) lanzó una convocatoria de respuesta rápida al coronavirus, la cual invitaba a grupos de investigación a proponer proyectos relacionados con la pandemia.
En mi caso, fui invitado a participar de 4 proyectos en calidad de coinvestigador. Estos proyectos fueron propuestos por docentes e investigadores de la Facultad de Ingeniería Eléctrica de la UTP (FIE-UTP) en la cual yo trabajo. De estos 4 proyectos, 2 fueron seleccionados para ser financiados por la SENACYT. Uno de esos dos proyectos consistía en el diseño y construcción de un ventilador de bajo costo en respuesta a pandemia provocada por COVID-19.
Paralelamente se formó la iniciativa de Ventiladores por Panamá. Debido a que los fondos de SENACYT son públicos, existen procedimientos burocráticos que impiden que el dinero sea entregado a los grupos de investigación de manera rápida. Con Ventiladores por Panamá se buscaba empezar el proceso de diseño y construcción de los ventiladores, para lo cual se convocó a los investigadores que hicieron propuestas relacionadas al tema de respiración artificial. También se tomó en cuenta a profesionales con experiencia en áreas afines, con lo cual se conformó un grupo numeroso de personas dispuestas a trabajar en este proyecto. La iniciativa fue convocada por miembros de la SENACYT, INDICASAT, UTP y el Presidencia.
En mi caso, no formé parte de la iniciativa en un principio. Yo me involucré en la iniciativa luego de que el Dr. Alejandro Von Chong, docente en FIE-UTP, el investigador principal en la propuesta que se presentó a la SENACYT, me pidió que lo apoyara con la construcción de un prototipo inicial que fue propuesto por el Ing. Julio Grossman, miembro de la Fundación 100 Panas.
La Fundación 100 Panas es, básicamente, un grupo de amigos (100) que financian proyectos de 10,000 dólares en Panamá. Son 100 amigos que cada cierto tiempo se reúnen y aportan 100 dólares, cada uno, para financiar algún proyecto de cualquier persona que exponga algún proyecto en una de sus reuniones. O algo así. Eso fue lo que le entendí a Julio Grossman.
El ingeniero Grossman propuso que se construyera un prototipo con base en un diseño de una universidad en Florida y, a partir de ahí, junto con el Dr. Von Chong, empecé a trabajar en esta iniciativa.
Bitácora del proyecto Flujo Contínuo, modelo UTP-100P
Para describir algunas partes de esta bitácora utilizaré las fechas y horas múltiples conversaciones en whatsapp que tuve con distintos miembros del equipo de trabajo. Estaré aportando imágenes y videos compartidos con los colegas para ilustrar los procedimientos realizados.
9 de abril de 2020: acercamiento inicial
A las 11:35 PM me escribe el Dr. Von Chong al Whatsapp para preguntarme si estaba disponible. Yo estaba dormido.
Me envió el siguiente enlace: https://simulation.health.ufl.edu/technology-development/open-source-ventilator-project/
También me envió la siguiente imagen:
Tengo entendido que este diagrama lo propuso Julio Grossman con base en una documentación publicada por la Universidad de Florida. Yo no contesté los mensajes sino hasta el día siguiente cuando desperté.
10 de abril de 2020: empezamos a trabajar
Contesté los mensajes a las 7:41 AM. Mi respuesta fue: «sí, tengo todo». Con los años que tengo en esto de hacer proyectos, he coleccionado una gran cantidad de componentes electrónicos para el desarrollo de casi cualquier proyecto de prototipado. Viendo el diagrama que compartieron con el modelo de la Universidad de Florida, esta es la lista de materiales que se necesitaban:
- Arduino Nano
- Pantalla LCD 16×2
- Regulador 5 voltios (LM7805)
- Transistor NPN
- Botón SPST (push button)
- Potenciómetro
- Resistencias y capacitores para la polarización del transistor y filtrado de voltajes.
Revisando en mis cajas de componentes encontré todo lo necesario, lo cual compartí en esta imagen:
Con los componentes en mano, ese mismo día se empezó a trabajar en el primer prototipo de controlador para el sistema. Según entendí, se necesitaba un controlador que permitiera abrir y cerrar una electroválvula de 12 voltios cada cierto tiempo, controlando el tiempo de apertura y la relación de tiempos entre cierre y apertura.
El concepto detrás del respirador de flujo continuo es el siguiente: se aprovecha la línea de aire presurizado de los hospitales para la respiración del paciente. Utilizando un sistema de tuberías que se conecta a la línea presurizada, con abrir y cerrar una electroválvula se puede inyectar aire al pulmón de un paciente y permitirle hacer la exhalación.
El Ing. Julio Grossman se encargaría del sistema de tuberías, utilizando tubos de PVC y una electroválvula de jardinería (en ese momento no teníamos idea alguna de lo que era respiración, compatibilidad con oxígeno, normas de seguridad, etc). Se trataba de un concepto muy sencillo y, por lo tanto, adecuado para situaciones de emergencia.
Por mi parte, había que construir el controlador. En aquellos días yo había solicitado permiso a la Universidad para llevarme algunos equipos de impresión 3D y la impresora de circuitos CNC a mi casa, pues habíamos entrado en cuarentena total y no era posible seguir con mi trabajo en mi oficina en la Universidad. Gracias a que se me permitió llevarme algunos equipos a casa, pude dedicarme a construir el prototipo del controlador aquel mismo día. También empecé con la fabricación de face shields, pera esa es otra historia.
Se hizo un diseño en EasyEDA y pronto se procedió con la construcción de la primera tarjeta de control.
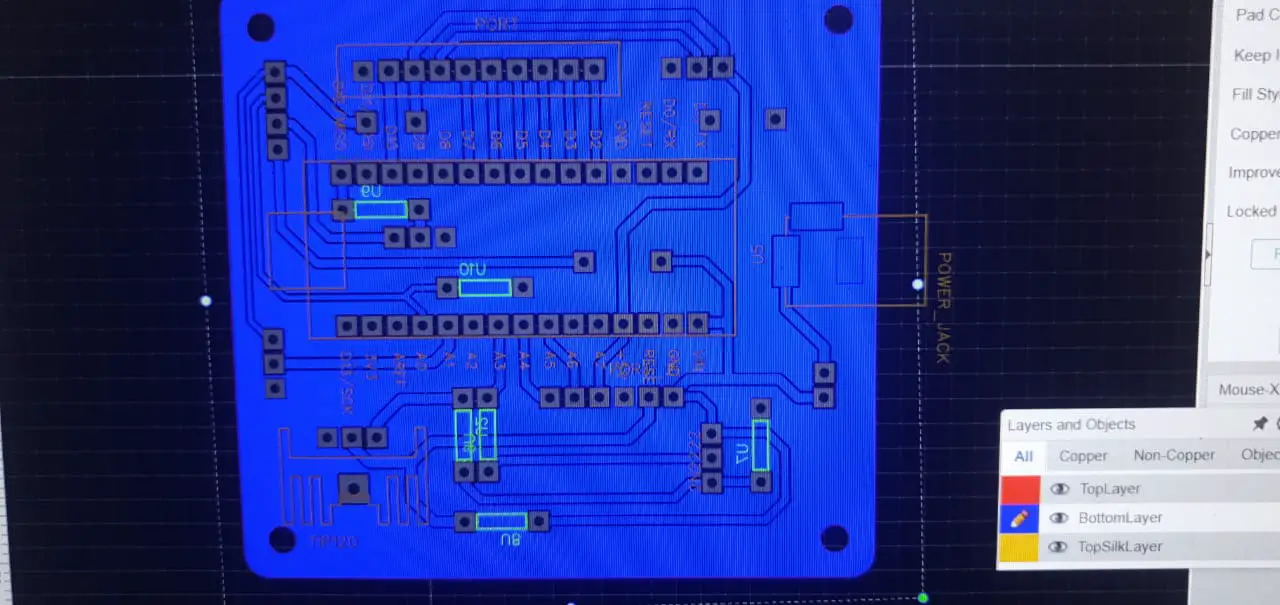
Se utilizó el Router CNC Othermill que tenemos disponible en la Facultad de Ingeniería Eléctrica para construir la tarjeta.
Las tarjetas quedan bastante bien, y el proceso solamente dura unos 20 o 30 minutos, en el caso de esta placa que no es muy grande.
A estas tarjetas hay que darles un tratamiento adecuado para evitar la corrosión. Eso debería hacerse con un papel especial o con tintas de curado ultravioleta, pero por lo pronto se utilizó un recubrimiento de estaño con el MG Chemicals Liquid Tin 421. He aquí un clip de video con el proceso.
Aunque el estaño líquido no es el químico apropiado para este procedimiento, yo lo utilizo como una forma rápida de resolver el problema de la corrosión. Las placas se ven muy bien después de este proceso y permanecen así durante un buen tiempo.
A las 1:58 PM se había llegado a este punto. En 5 horas ya teníamos un diseño y una tarjeta construida.
A las 5:37 PM ya estaba soldada la placa principal. La alimentación de este circuito se haría a través de un adaptador de 12 voltios que se conectaría al jack que se muestra en la imagen de arriba en la parte de la derecha. Los 5 voltios para el funcionamiento de la pantalla LCD saldrían del regulador de voltaje del Arduino Nano. El circuito contaba con una salida de potencia de 12 voltios controlada por un transistor 2N2222 para la luz de retroiluminación del pulsador. La salida de potencia de la electroválvula sería manejada por el transistor TIP122, con sus respectivo diodo de protección y disipador de calor. Cuenta con una entrada de un potenciómetro para controlar el tiempo de apertura de la válvula.
Hacía falta soldar el módulo de la pantalla LCD.
A las 9:31 PM ya estaba listo el módulo de LCD. Se utilizó un bus de cables con cabezales JST para la interconexión rápida y correcta de los módulos. Paralelamente a la construcción del circuito se diseño un prototipo de carcasa protectora para ser impresa en 3D.
A las 11:07 PM está lista la tapa de la cajita, en la que se incrusta la pantalla, el potenciómetro y el pulsador. Aún hacía falta imprimir la base de la caja, pero con la tapita ya era posible hacer pruebas para verificar dimensiones y robustez de la carcasa.
Para ser el primer día de trabajo, creo que se logró avanzar bastante. Fue un buen día para trabajar y tratar de empezar con el pie derecho.
11 de abril de 2020: segundo día de trabajo
A las 3:03 AM se terminan los primeros ajustes para comprobar el funcionamiento de los periféricos del prototipo: se comprueba el funcionamiento de la pantalla LCD, del pulsador y del potenciómetro.
A esta hora me fui a dormir un rato. Había estado trabajando ininterrumpidamente desde la mañana del día anterior.
A las 7:30 AM me despierto y verifico si la impresora 3D había finalizado con la construcción de la base del prototipo. En este procedimiento se utilizaron dos impresoras en paralelo: una Prusa MK3S y una BCN3D Sigma r17, ambas propiedad de FIE-UTP.
La caja no me quedó bien. El espacio vertical quedó mal calculado, por lo cual la tapa no cerraba. Aún así pude probar algunos conceptos de diseño que utilicé y empecé a rediseñar para ajustar las dimensiones a los componentes de hardware. Aquí les dejo algunas imágenes de cómo quedó la caja con el circuito montado.
[Best_Wordpress_Gallery id=»37″ gal_title=»utp100p_1″]
Durante aquel día se trabajó en el mejoramiento del diseño y se puso a imprimir la nueva pieza en la impresora 3D.
13 de abril de 2020: finalizado el primer prototipo
Luego de dos días se cuenta con un diseño final en una caja impresa en 3D, atornillada, que cuenta con una entrada de energía y una salida de potencia a través de un puerto ethernet (RJ45). Se decidió utilizar el puerto ethernet para la salida de potencia pues ofrece una interfaz de conexión rápida entre el exterior y el interior del dispositivo.
Aquí les comparto un video del prototipo ya impreso, sellado y atornillado.
La caja quedó bastante bien. La impresora 3D (Prusa MK3S) hizo un excelente trabajo. Mis diseños los hago en Autocad y decidí darle esa forma a las esquinas para poder aumentar el grosor de pared alrededor de los tornillos.
Utilicé tornillos Phillips M4 de 1/2″ de largo. Estos tornillos permiten agarrar la tapa de la carcasa desde la parte de abajo. A la hora de diseñar con este tipo de tornillos se recomienda dejar un hueco de un grosor de 2.8 mm en la carcasa 3D para que el propio tornillo haga la rosca en el plástico. Esto es válido para tornillos M4.
Siempre procuro dejar un grosor de pared mínimo de 2 mm alrededor del tornillo para que cuando se haga la rosca, el tornillo quede bien adherido a la carcasa. En las carcasas dejo un grosor mínimo de pared de 4 mm, lo cual hasta ahora me da buenos resultados. En la base utilizo 5 mm de grosor.
Los parámetros de impresión para carcasas pequeñas como la del video es de 0.2 mm de grosor de capa, junto con 2 mm de shell y 30% de infill. Siempre utilizo PLA para impresiones de este tipo.
15 de abril de 2020: primera reunión presencial con los miembros de la iniciativa Ventiladores por Panamá
Este día se produjo la primera reunión en la que participaron múltiples miembros de la iniciativa Ventiladores por Panamá. La reunión de produjo en la UTP en el edificio de la Facultad de Ingeniería en Sistemas Computacionales, salón 3-210, a eso de las 4:00 PM.
Antes de la reunión conocí a Julio Grossmann en persona y probamos el prototipo del controlador con el prototipo del sistema neumático, el cual estaba hecho con tuberías de PVC. He hecho este diagrama para ilustrar la idea:
Y aquí les dejo el video de nuestra primera prueba:
Este sistema tiene un principio de funcionamiento muy sencillo: cuando se abre la electroválvula, el aire fluye hacia el paciente, mientras se llena el globo que está en la salida de aire. Ese globo tiene la función de evitar que el aire salga del sistema en el tiempo de inspiración. En el tiempo de expiración, ese globo debe haberse desinflado y debe permitir la salida del aire.
Cuando conectamos el controlador digital a la electroválvula, conectamos el sistema a un compresor de aire que tenemos disponible en la FIE y empezamos a probar. Aparentemente funcionaba bien, al menos en cuanto al objetivo de llenar y desinflar el globo. Estábamos muy contentos con lo logrado hasta este momento pero, siendo sincero, no teníamos la más remota idea de lo que estábamos haciendo e ignorábamos muchos conceptos que debíamos tomar en cuenta en este proceso.
En la reunión de las 4:00 PM llevamos un video de la prueba que habíamos hecho aquella tarde y rápidamente nos dimos cuenta que teníamos que mejorar nuestro diseño.
Aquel día contábamos con la presencia del Dr. José Trujillo, médico intensivista, quien tiene mucha experiencia en cuanto a respiración artificial. Aquel día empezamos a aprender sobre conceptos como presión en la vía respiratoria, volumen tidal, flujo volumétrico hacia el pulmón, formas de onda, formas de control de presión y volumen, entre otras cosas muy interesantes sobre el tema de respiración, el cual era un nuevo mundo para mi en ese momento.
A la reunión asistieron otros equipos de trabajo de otras unidades académicas dentro de la UTP, así como otras universidades y empresas del sector privado. Todos los equipos mostraron algunos de sus avances en sus prototipos y se dio una sesión de intercambio de ideas sobre conceptos importantes a tomar en cuenta a la hora de diseñar equipos médicos.
En este intercambio de ideas nos hicieron algunas observaciones:
- El PVC no es compatible con oxígeno. En las terapias respiratorias a veces se utiliza concentraciones de oxígeno que llegan hasta el 100%. El PVC puede reaccionar con el oxígeno y formar compuestos tóxicos que pueden ser perjudiciales para los seres humanos.
- La electroválvula debe ser compatible con oxígeno. El material debe ser compatible con oxígeno, no debe utilizar grasa y no debe provocar chispas, pues en un ambiente enriquecido con oxígeno una chispa es extremadamente peligrosa. La grasa que utilizan algunas electroválvulas para su funcionamiento reacciona con el oxígeno, lo cual podría causar una ignición.
Debemos recordar que a este punto apenas teníamos una semana de haber empezado este proceso y aún ignorábamos muchas cosas asociadas a la construcción de equipos médicos. Con esta reunión nos dimos cuenta que no podríamos usar PVC y que la electroválvula debería ser diseñada especialmente para uso médico.
Podemos decir que a partir de este día fue que empezamos a tener una idea más clara de lo que había que hacer. Decidimos tratar de buscar a alguien que nos ayudara a hacer el sistema con tuberías de acero inoxidable, algo que resultó imposible en el mes de abril, a tres semanas de haber iniciado la cuarentena total.
También decidimos buscar válvulas de uso médico, pero no encontramos disponibilidad en las tiendas en Internet. Hacía falta investigar un poco más.
16 de abril de 2020: simulando respiraciones con un LED
Este día se grabó un video con una simulación sencilla en la que se utiliza un LED a modo de salida digital para simular el tiempo inspiratorio y la relación de inspiración y exhalación. Hasta ahora se supone que lo único que tiene que hacer el prototipo es controlar una salida digital de 12 voltios, la cual se conecta a la electroválvula que será utilizada para controlar el flujo de aire.
Por ahora se ha hecho una simulación sencilla utilizando como salida digital un LED. He aquí el video de la simulación.
El cable de Ethernet permite la conexión entre el controlador y un adaptador al cual se conecta la carga que se desea controlar. El potenciómetro permite modificar el parámetro «ti» (tiempo inspiratorio) y con el botón se cambia «Rel. i/e» (relación inspiración/exhalación). «te» (tiempo de exhalación) es una consecuencia de los dos parámetros anteriormente mencionados.
19 de abril de 2020: mejoramiento del controlador digital
Se hicieron mejoramientos al controlador, pues en ocasiones, al probar la versión anterior, se daban situaciones en las cuales el controlador se congelaba y la pantalla LCD mostraba caracteres aleatorios. La conclusión a la que se llegó es que al encenderse la electroválvula, una carga inductiva, se producía un «bajón de voltaje», el cual afectaba el microcontrolador y la pantalla LCD.
Para corregir esto se decidió agregar algunos capacitores entre la alimentación de 12 voltios y tierra, para evitar fluctuaciones importantes de voltaje durante la conmutación de la electroválvula. Se hizo un nuevo video probando el controlador esta vez con una electroválvula:
El controlador ahora soporta las variaciones de corriente que povoca la electroválvula. Funciona bastante bien.
20 de abril de 2020: primeras pruebas funcionales en CREAS
En este día se hicieron las primeras pruebas funcionales en CREAS. Hasta ese momento no se había podido hacer mucho con las tuberías, así que fuimos con el prototipo hecho en PVC para probarlo con los pulmones artificiales disponibles en el CREAS de Ciudad del Saber en Clayton.
En el CREAS se reunieron los equipos que estábamos trabajando en ese momento junto con el Dr. Fernando Alfaro, otro médico intensivista que, al igual que el Dr. Trujillo, se ofreció voluntariamente a apoyar esta iniciativa.
Estando allá ese día se logró establecer contacto con el Lic. Baltazar Moreno, quien es gerente de la empresa Aceti-Oxígeno, S. A. (AOSA). Esta empresa es, básicamente, la empresa líder en el mercado panameño en cuanto a gases médicos, tanto suministro como en diseño y construcción de instalaciones. Tienen mucha experiencia en este campo y cubren la mayor parte del mercado panameño, incluyendo a la mayoría de los principales hospitales en Panamá.
Baltazar se ofreció a apoyar nuestro proyecto en la construcción de un sistema con tuberías de cobre, compatible con oxígeno. Con la experiencia y el apoyo del personal técnico de AOSA tendríamos la oportunidad de adaptar el diseño neumático a las exigencias de los sistemas médicos, un paso muy importante desde el concepto inicial hacia un prototipo funcional formal.
27 de abril de 2020: prototipo de sistema neumático hecho en cobre
Con el apoyo de AOSA y de Baltazar se logró armar el primer sistema neumático en tuberías de cobre, el cual se muestra a continuación:
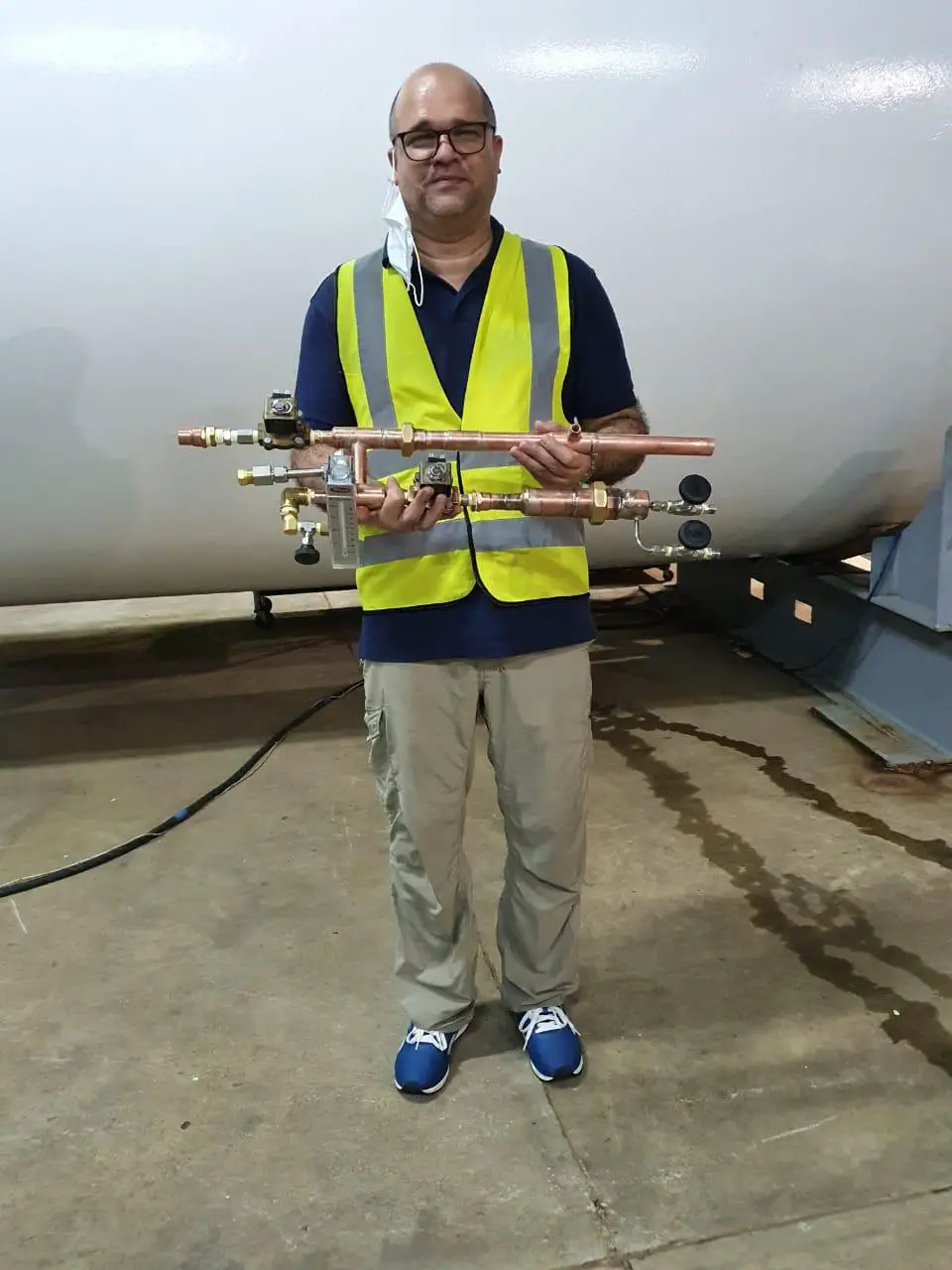
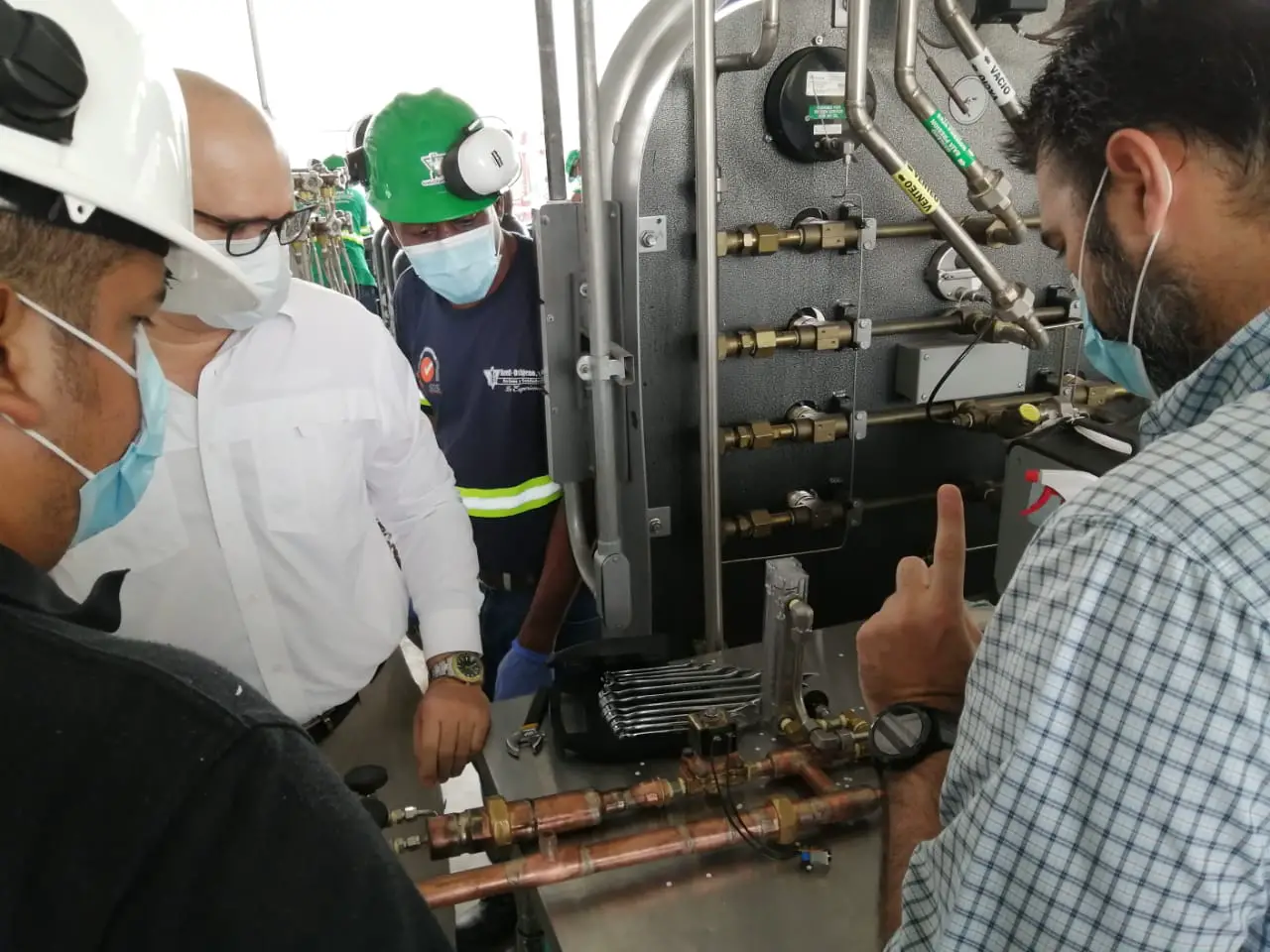
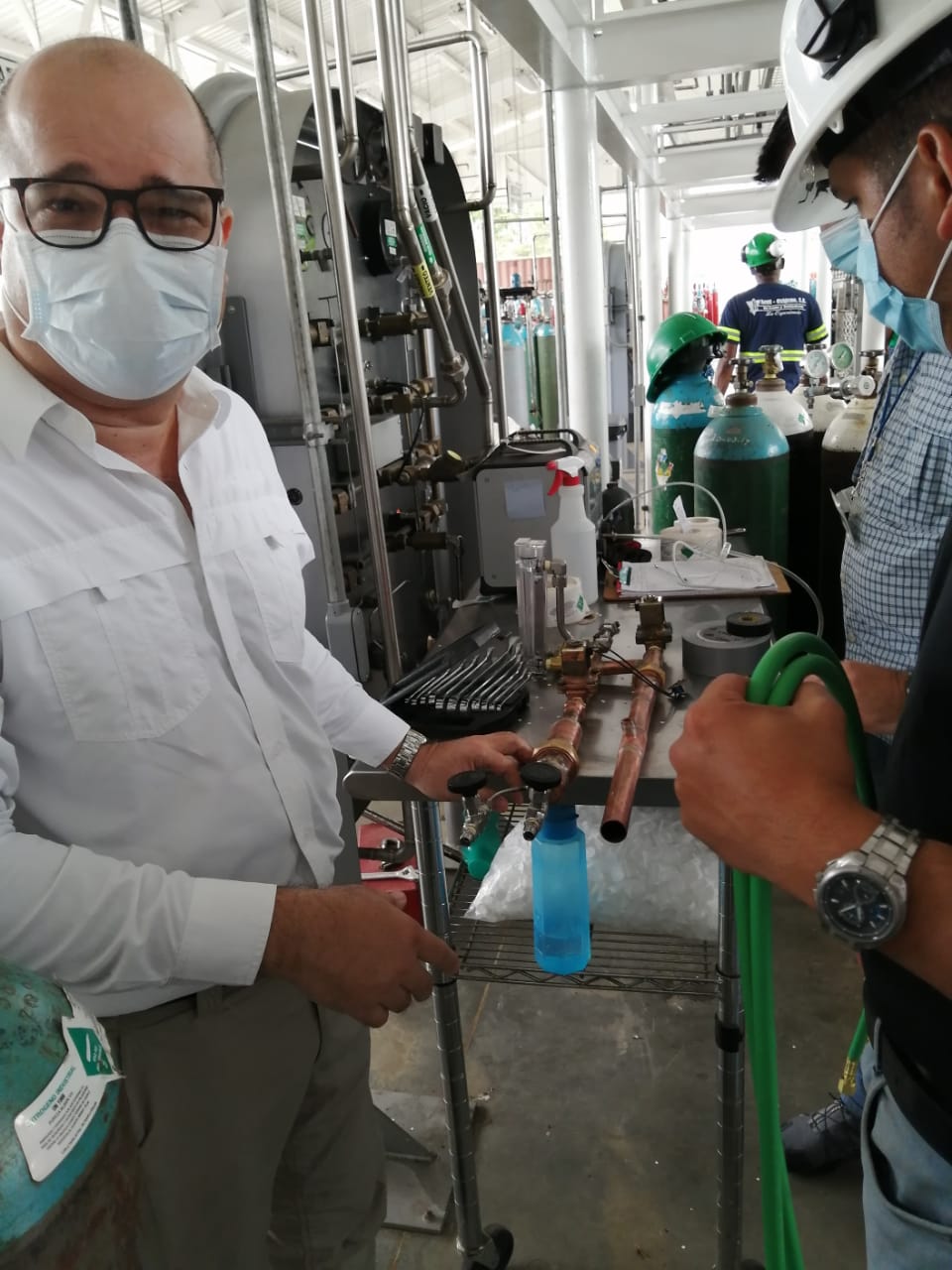
Con este nuevo diseño se buscaba resolver lo de la compatibilidad con oxígeno, tanto en las tuberías como en las electroválvulas. Se pasó de utilizar una sola válvula a usar dos, una para inspiración y otra para expiración. Eso, por supuesto, requirió de un rediseño en el controlador.
3 de mayo de 2020: nuevo controlador
En este punto se diseñó un nuevo controlador en el que se aumentó drásticamente la capacidad del controlador, tanto en tamaño como en complejidad. Se empezó a considerar el uso de sensores de presión diferencial para medir tanto la presión como el flujo en la vía aérea, utilizando para ello el efecto Venturi. Los sensores que se consiguieron en ese momento producían una señal analógica muy pequeña, razón por la cual se empezó a considerar el uso de un ADC más rápido y preciso que el del Arduino Nano que se estaba usando en ese momento. El dispositivo que se consideró fue un ADS1115:
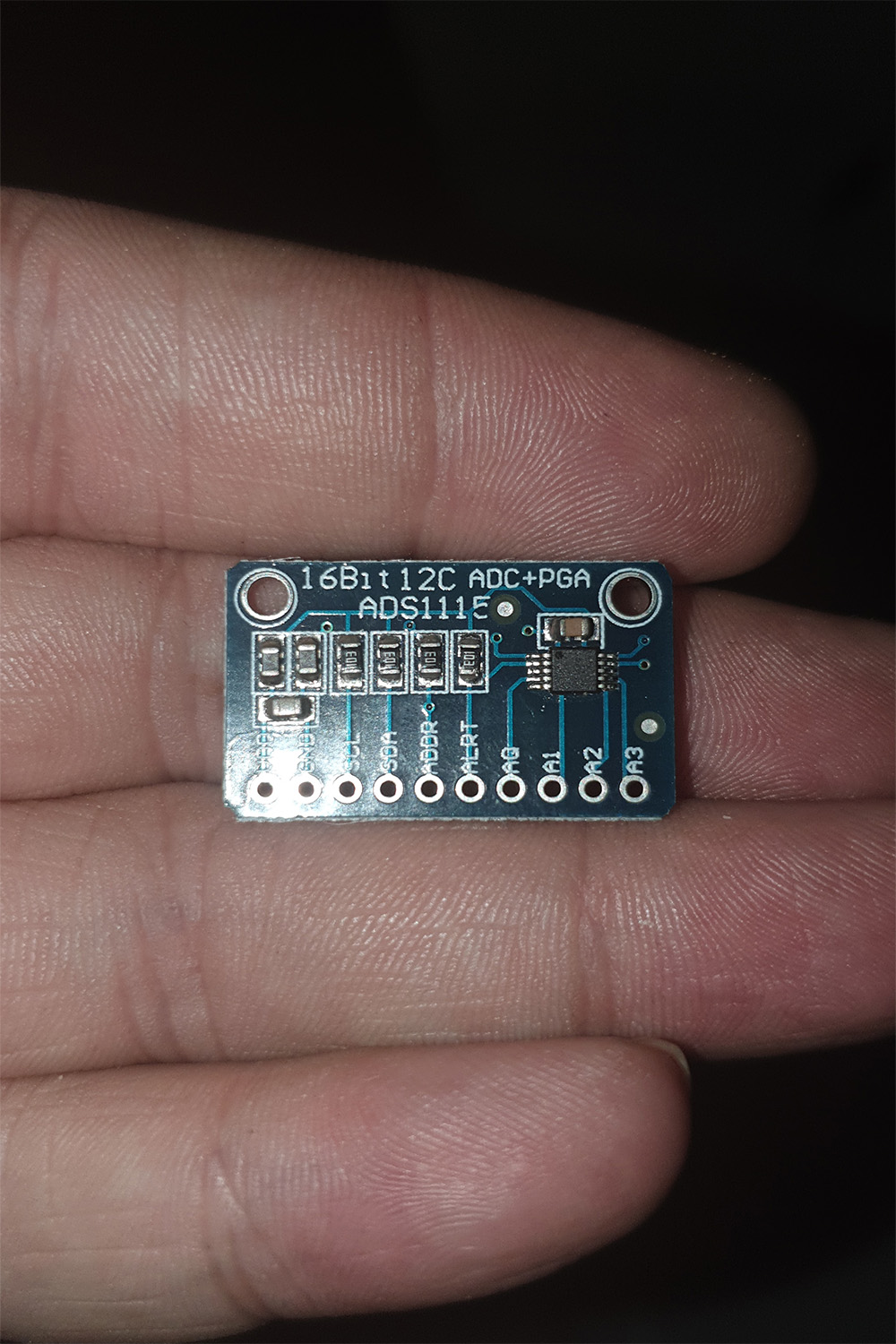
Como ya mencioné antes, la placa del controlador creció en tamaño y complejidad:
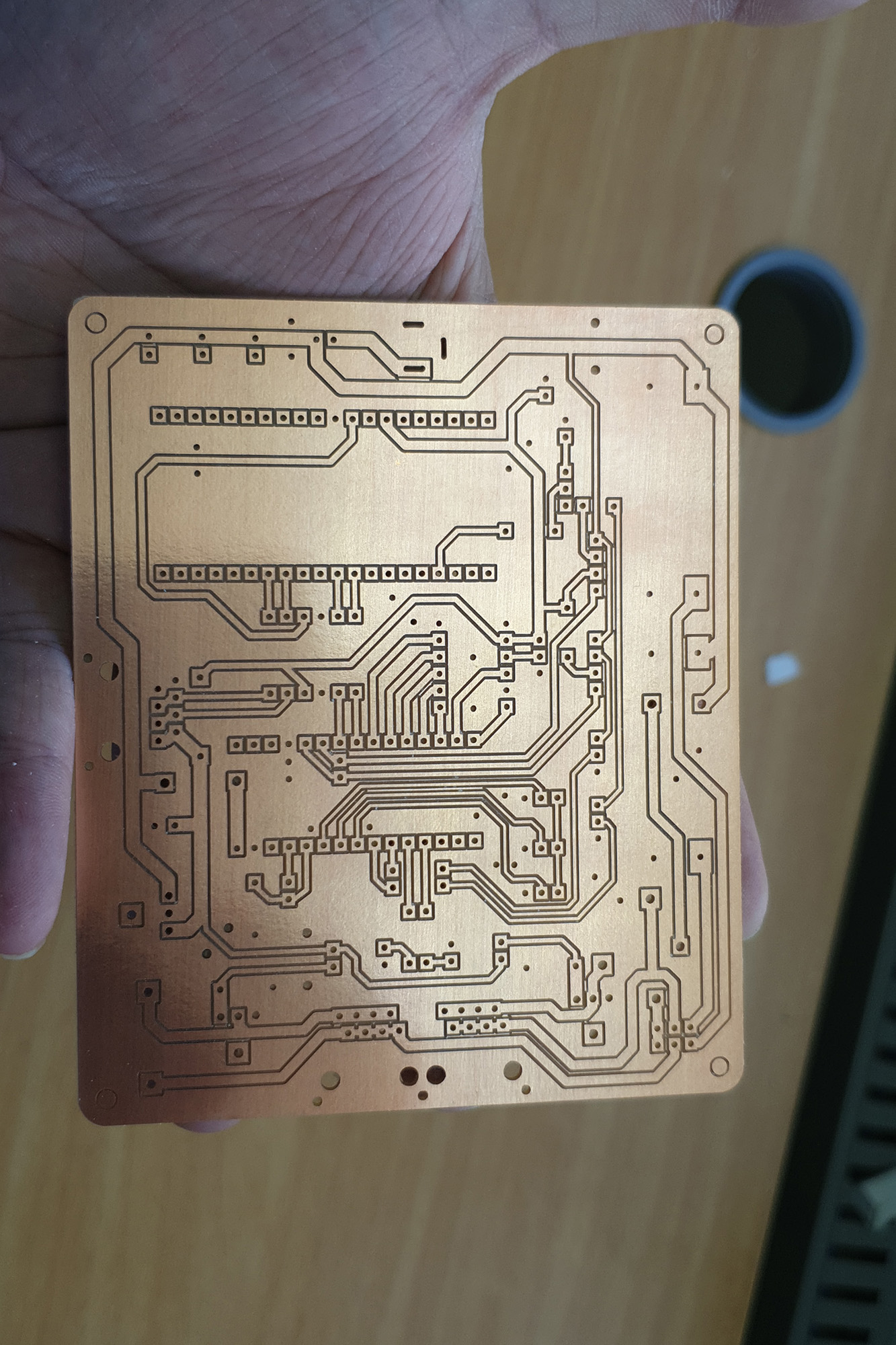
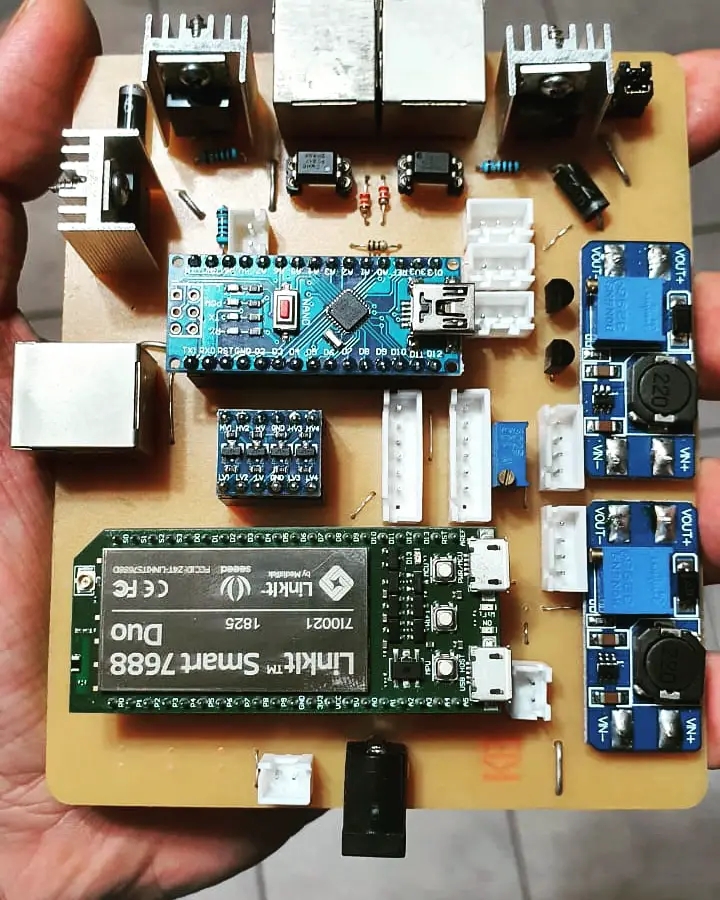
Este prototipo contaba con las siguientes características:
- Alimentación de 12 voltios, regulada a 5V con un 7805.
- Dos microcontroladores y un microprocesador: un Arduino Nano y un Linkit Smart Duo 7688.
- Una entrada de datos para leer los sensores (ethernet)
- Dos salidas de potencia para controlar las electroválvulas (ethernet). Las salidas son transistorizadas (MOSFET) y controladas por medio de optoacopladores.
- Dos elevadores de voltaje, de 12 a 24 voltios, para alimentar las electroválvulas
- Entradas y salidas para botones con luces y una pantalla LCD de 16×2 (JST)
- Convertidor de niveles lógicos para la comunicación entre Arduino y Linkit.
Sobre estos componentes tengo algunas observaciones:
- Los elevadores de voltaje no sirvieron. Se quemaron a la primera prueba con las electroválvulas porque la corriente de carga era superior a la que podían entregar. Como no tenía otro tipo de elevador, se terminó controlando las electroválvulas con 12 voltios, pues no había manera de elevar el voltaje o de trabajar en 24 voltios en ese momento. Con 12 funcionaban bien, aunque siempre se creyó que eso hacía que se sobrecalentaran las válvulas.
- El propósito de usar dos cerebros era el de dividir las tareas de muestreo, control y visualización de datos. Se decidió usar el híbrido entre Arduino Nano y Linkit debido a que con el controlador se incluye un procesador en el cual corre una distro de OpenWRT, siendo esto especialmente útil para tareas de procesamiento y almacenamiento de datos. Con el Nano se esperaba controlar las salidas y visualizar información en la pantalla LCD, mientras que con el Linkit se esperaba muestrear y procesar datos.
- El propósito de usar puertos de Ethernet es el de tener una interfaz que permitiera conectar elementos exteriores al interior del prototipo, de una manera fácil y rápida. Los cables de Ethernet permiten hacer eso.
Este prototipo se probó brevemente y, como veremos más adelante, sería desechado en favor de otros modelos que fueron aumentando su complejidad y poder de procesamiento a medida que las exigencias del proyecto lo iban requiriendo.
5 meses después…
20 de octubre de 2020: un vistazo al modelo final en televisión
El día de hoy ha salido al aire la entrevista a la cual se me invitó en SerTV en el programa Hashtag. Me han compartido la imagen promocional en redes sociales:
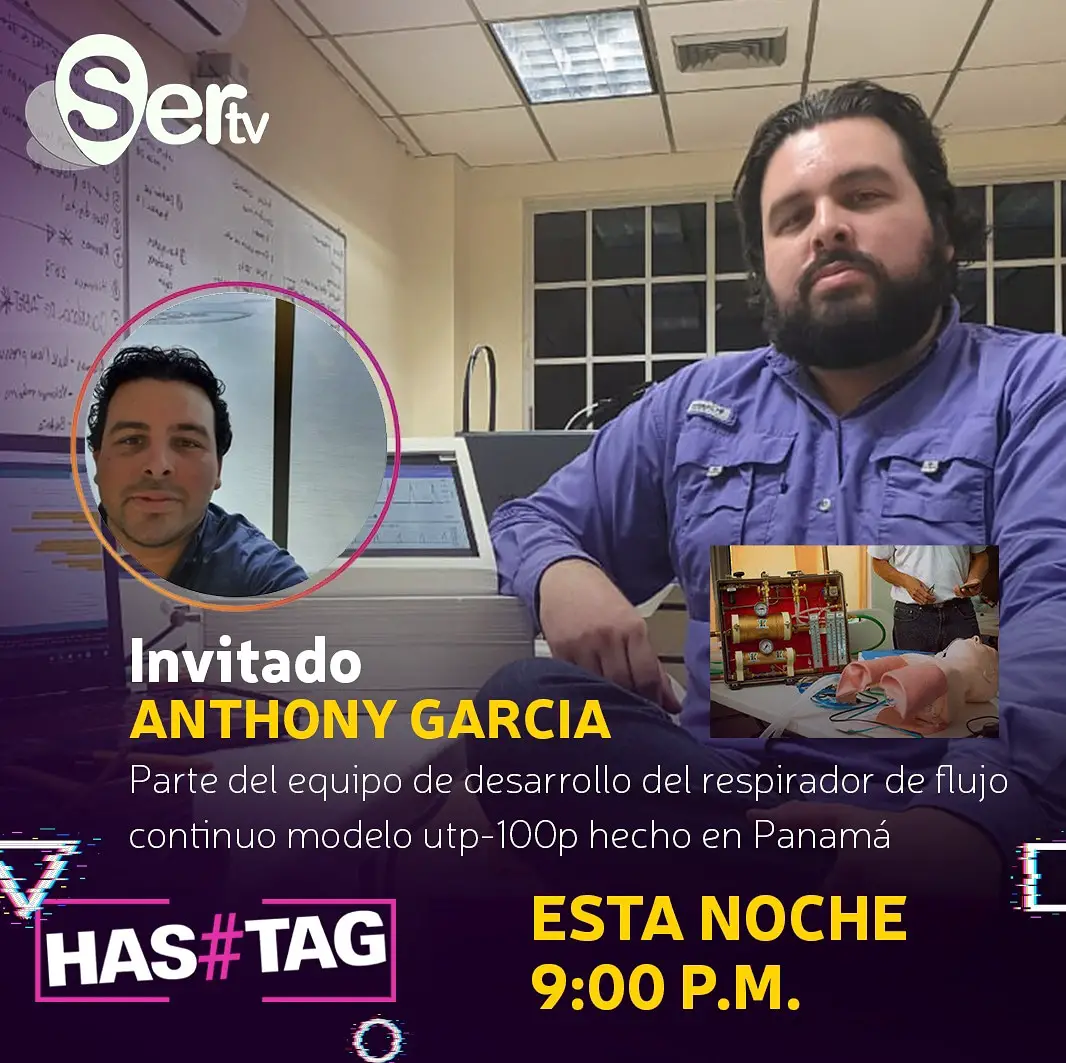
La entrevista se transmitió por SerTV a las 9:00 PM. Aquí les comparto mi participación dentro del programa, con una demostración en vivo del funcionamiento del prototipo:
Fue una experiencia interesante. Me tocó tratar de resumir el trabajo de los últimos 6 meses en unos cuantos minutos, tratando de mencionar a todos y cada uno de los participantes de este proyecto, sin los cuales no habría sido posible llegar hasta el final.